Timeline
D-Day (D is for delivery)
Wednesday 5th July 2017
On the eve of D-Day I called around the various parties involved - Watchet Marina, Interboat - the delivery driver and Tonhout, the crane driver at 'home' end, just to check all was ready. Everything was set; there was a weather window; nothing could go wrong. I took up my advanced position near Bristol, ready for the short drive to Watchet with nephew and photographer, Alex.
Alex and I left bright and early, looking to arrive at the harbour for coffee and bacon butties at 0800. At 0745 I got a call from a rather distressed lorry driver seeming to say that there was no-one available at Watchet to drive the crane. But I had confirmed the 'lift' the night before - surely some mistake. Several increasingly annoyed phone-calls later, I had to dismiss the delivery driver and escort vehicle as it became apparent that the lift was, indeed, not going to happen that day.
Whilst waiting for the Marina Manager to return, Alex and I spent a lovely sunny morning in charming Watchet completing seven of the eight 'Things To Do In Watchet' as recommended by the Town Council. (For the curious, the eighth was 'Go on a fishing trip aboard 'Scooby Doo'. For the first seven, I suggest you spend a very short amount of time in Watchet...) Sadly, none of the 'things to do' was to strangle the Marina Manager. Shame.
One fraught conversation and several more phone calls later, D-Day was postponed for 24 hours. So, back to my billet in Bristol for another (very enjoyable) evening with my kind hosts with everything set for the following morning.
Thursday 6th July 2017
Having been coerced into a second day in sunny Somerset with the promise of another bacon butty, Alex and I arrived back in Watchet hopefully to oversee the safe loading of 437 onto the low-loader to be delivered to her new life on a farm about as far from the sea as is possible on this small island.
The contrast with the day before was startling. The marina staff were efficient, working as a well-drilled team under their leader, Ian Lambert, and with minimal fuss 437 was loaded on, strapped down and ready to go.
Saturday 1st October 2017
MOVING DAY
Moving Day is finally here. Everything has been done that can be done in preparation for today. I have built scale models and 437 will fit through the side portal of the barn… but its tight. Very tight. By my calculations we have three inches clearance at the lintel and 1.5 inches clearance between the uprights. The problem is that once the transom is flat against the back wall of the barn, there is still twelve feet of boat still sticking out into the yard.
The trolley I have had built has been fitted with small, high loading casters; this will enable us to move the boat in any direction, unlike axle steering. The plan, therefore, is to reverse more or less straight in until we hit the back wall then pull the stern sideways whilst allowing the curved shape of the prow to stay as close as possible to the right hand upright of the barn. She will fit. She must fit.
Getting the trolley into position was fiddly, but straightforward. The plan was simply to jack the bow of the boat up, adjusting the stands as we went (just in case) until we had sufficient clearance to slide the trailer in from the stern. It wasn't without its moments but went, more or less according to plan.
The first obstacle is that she is facing backwards on the hardstanding so we need to turn a 42ft long boat around on 35 ft of hardstanding. There is a building at one side, which limits our available space and mounds of rubble to the other side. Using a tractor as motive power, along with 'man' power we just managed to get her around. At one point, the prow was tight against the building and the stern was dug into the rubble. Close call, but 'challenge one' surmounted.
The route into the barn involves going over a particularly deeply rutted patch of soft ground. We have filled the ruts with scalpings and laid 3/4 ply over the top to give us a surface. Once the trailer hit this surface there was a lot of crunching sounds as the small wheels crushed the ply but she moved fairly easily. Just as I was starting to feel confident, the trailer drifted sideways onto a part of our trackway that had ply but no scalpings and with a ghastly splintering sound, the caster half disappeared through the ply wood. Bugger. I hadn't planned for this.
There was only one thing we could do. We positioned the jack under the beam of the trailer, jacked the trailer up so the caster was clear and then moved the trailer forward using the arc of the rotating (collapsing!) jack to carry the caster onto 'solid' ground, six inches away. This was a nailbiting moment; at one point, the trailer was on two wheels. Bearing in mind it was built for five tonnes distributed over four wheels, having all the weight bearing down on two wheels was a very anxious moment for us all. If the trailer has given, I would be the owner of a broken trailer and some very expensive firewood. It is testament to Ed and Paul's engineering skills that this didn't happen - the trailer held and performed impeccably through the whole move. Hats off to you, Gents.
After that bit of excitement, the final manoeuvre into the barn was relaltively trouble-free. The clearances were exactly as caluculated and there was much shaking of heads but I had confidence that she would fit, and she did.
ST437 is now in position and restoration work can start in earnest.
The whole move went remarkably smoothly and mostly according to plan. I must pay tribute to the five Gentlemen who turned up on this Saturday morning to help with the move: Ed and Paul, who also built the trailer; Baron, my next door neighbour; Matthew who drove the tractor and Ian, an engineer of many years experience. Thank you chaps. I really couldn't have done it without you.
There is a video of the whole Moving Day on our YouTube channel. Search 'ST437 Restoration' on YouTube or go to: https://www.youtube.com/watch?v=fSpkogJMwV0&list=UUmsKzq-2XWaDz5UchMj8ujg&index=2
October and November 2017
STRIP OUT
Having got her into the barn, most weekends over the last couple of months, we have been stripping out practically everything from 437, taking her all the way back to the hull. One of the most charming jobs was removing all the dried sludge in the bilges - nasty sticky, oily goo about two inches thick. We have also taken out all of the fixtures and fittings - I have an extraordinary selection of fairleads, cleats and other deck fittings, all swathed in countless layers of paint in a rainbow of different colours, most recently red oxide. Didn't stop the deck rotting!!
Taking the rudders out was interesting - thanks Baron. I hadn't noticed earlier but the rudders are different shapes - that must have helped her handling. We have left the rod that connects the steering mechanism to the rudders in place; they'll be one of the last things to go as they run under everything else.
As the hull paints flakes off more and more 437 is revealing more of her secrets: there is a significant repair amidships on the starboard side. There is a board that has been inlaid vertically across the diagonal planking which has then been covered with a piece of stainless steel. Predictably, it crosses the three longest planks on the entire hull. It has also become apparent that the aft-peak is going to need re-building. There are some major repairs that have been carried out at some point. Maybe this was the 'damage' referred to in the Admiralty sale catalogue..? It'll be fun, anyway. I am actually looking forward to it.
Gordon Leith, a Curator at RAF Hendon Mueum, has been very helpful in sourcing original drawings and other information. I now at least have some drawings that give me an idea of what she should look like.
There is a little more stripping out to do - bulkheads followed by the coachwork and then it will be time to start concentrating on the hull. We will have all the paint sand-blasted off so we can make a full appraisal of the hull and establish how many boards will need replacing, whether the underside is sound - all sorts of critical information like that.
December 2017
MORE STRIPPING OUT
The laborious process of stripping out continues. It should be this difficult but nine out of every ten screws either is broken or breaks when you apply any pressure to it. I was given the hot tip of tightening the screw slightly before loosening it and this has marginally improved my success rate, but it is still problematic. It also doesn't help that this boat is incredibly well made and the original builders put her together in a particular order, not necessarily the same order (or opposite...) that I am taking her apart. All good fun!
Another interesting note is that, when they built these boats, they obviously had the mill make up lots of boards in a small number of standard thicknesses - 3/8" and 5/8" being the most prevalent - and when they need 1" timber, they laminated one of each board together, or 1 1/4", 2 x 5/8 boards, etc. Very clever but it makes dismantling tricky as the lamination appears, in some instances, like the saloon seating, to have been done in situ.
Timber!
Today the new timber arrived so we can start re-planking the hull. Lots and lots of 5/8th inch utile - very similar to, but more environmentally friendly than, mahogany. (Who mentioned cheaper?) You may recall back in April I had Marine Surveyor, Tony Tucker, survey the entire boat. One of his many recommendations was that a number of planks needed replacing. Well, having considered the options, I have decided to replace all of the outer planks - i.e. the side planks and the outer layer of bottom planks. This will add months to the project (yippee!) and pounds and pounds to the bill (boo!) but will do justice to Vera's hull and give her a proper, full life ahead. The fact is, if I have to remove and replace every screw, as they are all rotten, the thought of re-attaching the old boards seems bonkers.
Now, removing the planks is a seriously arduous task - in addition to the screws every three inches along the seams on each plank and the screws attaching the boards to the ribs, a previous owner decided to rivet infills on the inside of the hull between the seam battens, effectively doubling the thickness of the hull. I have given much thought as to why they did this... Judging by the amount of filler used, I think it must have been to stop water ingress. Only history knows if this was successful but if the waterline on the inside of the hull is anything to go by, it wasn't! Anyway, each board has around 24 screws and eight or ten rivets to remove.
Help, however, is on hand in the delightful form of my sister Jo. This is becoming a proper family affair (still no sign of my wife...). Jo, and her husband Justin (see April) came down for the weekend and spent a sizable chunk of their time here working on Vera. Jo has discovered that removing screws from an old boat is extremely therapeutic! As a result, she is perfectly happy to spend six hours with a screw-driver in one hand and a pair of snips in the other slowly removing, or trying to remove, rotten fixings.
END OF YEAR REPORT
Dame Vera Lynn. Year 2
The second year of the project has been a busy year for Vera and she continues to be an engaging and valuable member of the community. Well-liked by her peers (two enterprise dinghies and an inflatable), Vera is a pleasure to work on and we have high hopes that this will continue as we move into the next phase of her development. Vera needs to remain patient and focused on the end result and I have no doubt she will, in years to come, make a significant contribution to our national heritage.
Ribs and Frames
Much of Vera's time prior to joining us appears to have been spent repeatedly floating and then settling in a muddy environment - a harbour or estuary. She came to us with a marked tideline between her port-side chine and starboard gunwale, everything below this line was mud-caked. This was a mixed blessing: the majority of her starboard side ribs and frames were structurally sound, although needed a good clean-up, whereas the majority of those on the port-side were rotten and needed replacement. These were replaced in her Reception year, and the early part of this year, which created a solid foundation upon which later work has been based.
Topsides
Vera's topsides are now all but complete. She has been entirely re-planked with 16 mm utile which has been caulked and fully screwed down. The dry weather at the start of the summer has caused some of the boards to shrink a little but this will rectify once the traditional British damp arrives, well, any day now. The next stage for Vera's topsides is the fairing process which will be undertaken using West System epoxy and we envisage this taking place towards the end of the next build year.
On a personal note, replacing the topsides has been a very satisfying experience; labour intensive, admittedly, but the overall impact on her appearance has been very rewarding. At last we can once again see the beautiful lines of George Selman's inspired design. It almost seems like a shame to paint her.
Undersides
As was identified earlier in the project, repairing Vera's undersides was always going to be a difficult undertaking. The decision was taken, following the initial survey, not to replace all the boards, as we did with the topsides, but to only replace those boards which are damaged or have split due to drying out. This will be undertaken in the coming year.
Her undersides are double diagonal construction and we have had to make some repairs to the inner boards, notably at the prow and stern, but these are now ready for the work that lies ahead. Once this work has been done, we anticipate Vera's bottom being faired in the Spring term, along with her topsides.
Deck
Unlike many, Vera worked extremely hard during the covid lockdown. So much so, we have had to give her extra work not intended for this year group. This has included the decking. When she came to us in Year 1, Vera's decking was in a terrible state - it had been replaced, badly with plywood which had rotted extensively. This had had the knock-on effect of causing some of the structural elements to perish. Vera originally had a double diagonal mahogany deck, unlike many of her class, so the deck supports are relatively complicated. These have now been repaired or replaced and Vera is ready to receive the teak deck we hope to fit next year. Well done Vera.
Interior Structure
The interior structure does not form part of this year's syllabus, but Vera's application has meant that she has exceeded expectations in this area. The main structural components - the stringers - that run stem to stern, are intended to give her longitudinal rigidity. When she came to us, one of the pair of stringers was completely missing and the other in a poor state. These have both now been replaced - a significant milestone in Vera's career.
Furthermore, another key element of structure, her forward watertight bulkhead separating the fore-peak (and chain locker) from the wheelhouse, has also been replaced. The original handles to the hatch have been cleaned up and now sparkle once again.
Headmasters Report
Vera's contribution to my sanity over lockdown is immeasurable. She continues to be a most appealing distraction from the woes of the world and the day job. Vera is very popular - over 200 'likes' on Facebook - and is always the centre of attention amongst family and friends. She is well ahead of schedule and, going into her third year with us is a very exciting prospect with a re-vamp of her presence on Youtube and further exploration into fitting her with electric motors.
Vera, we expect great things from you...
Mid February 2021
All Strung Out
In my last proper post, back in June, I had just fitted the forward stringers. Well it looked so good, I just couldn;t resist pulling out all the nasty cockpit timbers and re-doing them. It was not originally part of the plan (as if I actually had one) to replace these but, having removed them, I am very glad I did.
The timbers that came out, and they are what gives Vera her rigidity, came out in pieces. Every one was broken in at least one place, the fixings that held the laminates together were all broken and, on reflection, it is easy to see how the port engine became out of alignment, resulting in catastrophic failure. New stringers have now been fabricated, same method as the forward stringers, and installed and it is a significant step forward.
You will also see from the picture that we have had to build a 'tent' around Vera in an attempt to create a tolerable working environment. We have reduced the volume of air around the boat by around 60% which will hopefully be easier to keep warm. I have three electric heaters, none of which is especially capable, using in excess of the 16 amps I have available to me. The upside is that I can keep the tent at 4 degrees above the ambient temperature elsewhere in the shed (usually a degree or two colder than outside!!). The downside is that I have to turn two of the heaters off if I want to use any other electrical equipment otherwise the electrics trip out. I now wish I had invested in 32 amp cable...
Another big 'win' of the year has been the acquisition of Vera's original searchlight. After three years of hassling, Owen Childs, the previous owner, finally came up trumps and we met at a socially distanced Gordano Services just before Christmas for the handover.
For me, this is a very important piece of the jigsaw and to finally get hold of the original is fabulous. I have been looking at various searchlights on t'internet for the last couple of years and none of them were quite right (and blooming expensive). This one is still painted in RAF grey and is entirely un-restored. At present it languishes on the floor on my dining room, along with my highly polished gear levers and beautifully restored steering wheel, as it will be one of the last pieces to be actually mounted on the wheelhouse roof, but I smile every time I walk past.
Other bits of progress include the replacement of some of the dodgy hull boards. My surveyor identified eight boards that needed replacement. I have slighly upped that number because I didn't like the look of one or two, but they are now well underway and the only limiting factor is how much time I want to spend lying on my back underneath Vera. It is incredibly difficult removing the hull boards as, just like the topsides, they have more fxings than Subway, only harder to get to. There are rivets, nails, screws, bolts and mastic all purporting to do the same job and all of which need to be removed. Thankfully, not so many need to be returned.
On the subject of topsides, I was fairly concerned in the summer that my beautifully fitted planks had shrunk during the warmer weather revelaing gaps of up to 3 mm. Fortunately, the return of proper English dampness has seen all of these gaps close back up again. Phew!
So, looking forwards (which I am loath to do): with luck and a fair wind, come April, when the weather begins to warm up, we will be first 'fairing' and then sheathing the hull. This is quite an undertaking, especially as I have never done anything more involved than repairing the keel on Quarry II. However, I have watched the West Systems video about ten times along with every similar video on YouTube (and there are many) so I feel adequately armed to tackle this first irreversible task. Once done, Vera will look amazing - more like a boat and less like a very expensive pile of timber - and I can't wait.
9th January 2022
I have rather ignored this webpage recently. With occasional posts going on my Facebook page I have totally omitted updates here.
Since the last post, which has been almost a year, much has been acheived. We missed the weather window for sheathing, so that remains an intention for 2022. I have talked about the width of the boards and the shrinkage: a 150 mm board of utile, with a shrinkage of up 3 percent, will leave gaps of up to 4.5 mm between boards when the weather drys out. I therefore have to time the caulking procedure quite closely.
When the gaps are at their widest - late summer - I need to apply the caulk into the gaps. This can be fairly tricky as the entire depth of the gap needs to be filled. Then, over the winter months, the boards expand again, closing the gaps and squeezing out the excess caulking, which has to be removed. And then the bit that requires timing: I have to paint the insides of the hull, to minimise moisture loss (and board expansion), fair the outside of the hull - itself a fairly delicate process to get right, and then, once I am happy with the fairing, apply the sheathing. The sheathing process needs warmer, dryer weather, but not soo warm or dry that the boards have started to shrink again. Timing is of the essence!
We have also been busy installing the bracing on the inside face of the hull. These are structural elements designed to help spread the loads between the chine and the gunwale, adding to the torsional strength of the hull. There are diagonal braces around the lifting points on each side - one forward and one aft - and smaller, vertical braces between each rib amidships.
As with much else this year, fitting these braces has been a laborious and not very glamorous task but, once fitted, a critical part of Vera's sea-worthiness... and it looks right, too!
You will perhaps remember the grief I have had with the oily bilges. Reportedly, the portside engine blew on a trip between Torquay and Watchet back in 2005, filling the bilges with dirty engine oil, adding to the general bilge gunk built up over 70-odd years of service. The legacy has been enormous quantities of oil, mixed with harbour silt, throughout the bilges especially, but not exclusively, under the cockpit/engine bays. The removal of this mess is imperative; it has soaked into the timbers which will make painting a near-impossibility. Nasty!
Ever since this project started we have been on a mission to remove as much of the oil as we can... for obvious reasons. It has been a three-part attack.
Part one, which started almost as soon as Vera was moved into the boatshed, was scraping the sludge out. It seems that Vera spend many of the tides before my acquisition settling on the Watchet Harbour silt at low tide and... erm... taking her time to re-float again. There was a dirty water line between the port chine and the starboard gunwale and everything below this line was very, very silty. That silt, plus the engine oil, had worked its way into every crack and crevice.
Part two was jet-washing, with various detergents and de-greasers - a task at which Baron excelled (and I avoided!).
Part three. It became apparent that it is the nature of timber, when it shrinks in drier conditions, to squeeze out oil that has soaked into the wood. In the summer, oil would ooze out, fairly freely, whereas in winter, it would appear almost oil-free. We discussed the benefits of 'Fullers Earth', or bentonite, to give it it proper name - basically cat-litter in powder form - that will absord any oil or other liquids. After a breif internet search, I found a supplier and did a limited test. Bingo! The bentonite went from a pure white powder to a nasty brown colour as it soaked up the oil. So part three was the liberal spreading of 25kg of bentonite (remarkably inexpensive) which was left in place over a few warm weeks. The results have been amazing - I only hope it will be sufficient when we start paint tests...
So that brings us more or less up to date. Most of the last three months have been focussed on the undersides. Without the facility to invert the hull, this has been done lying flat on my back - sanding, filling, sanding, caulking and sanding. A dozen or so boards have been replaced - rotten, split or with too many joints - so I am confident that, once complete, the hull will be sound.
Because most of the original fixings have rotted, I am having to re-fix everything. Rather than remove the existing screws and rivets, some of which are OK, I am instead fitting 'buddy' fixings, alongside the originals, with a few extras of my own. I never forget, one day Vera will go out to sea again; she has to be as strong as she was when first built.. or stronger.
The starboard side is more or less complete now so after another couple of months-worth of weekends I should have the port side done.
After that, it will be fairing, sheathing and painting - weather permitting...
June 2022
About time for an update...
First the bad news: All of my hard work on the undersides has been undone by the weather; not entirely, but annoyingly. Over the winter I splined all the gaps between the boards with the intention of getting her sheathed before the weather turned warm (and the workshop warmer). However, such was the time taken working on both the undersides and topsides, that when I went back to look at my beatifully prepped hull, the boards had already shrunk, breaking the bond between the old boards and the new splines. (To explain, utile has a shrinkage of around 3% so, as these boards are 150mm wide, I can expect shrinkage of up to 4.5 mm on each board. I did hope that the age of the boards - 80 years - would lessen the amount of shrinkage... I was proved wrong. In some respects, this is a good sign, as it means the fibres within the boards are in realtively good condition.) The upshot is that I will have to re-spline all the joints and make sure I get the sheathing done in a timely manner.
The next update relates to the oily boards. As reported above, I had great success with the bentonite, removing significant quantities of the oil impregnated into the bilge timbers. However, as the weather has warmed, the bilge boards have started 'sweating' out more oil. Another 25 kgs of bentonite on order. Hopefully, if I keep soaking up any secreted oil, I will finally end up with paintable boards...
I have discussed earlier my passion for peaning. Copper rivets were widely used throughout the original construction of Vera. They create a very strong mechanical fixing and will ensure that everything holds together under stress in a way that screws may not. Two key elements have now been (or are in the middle of being) rivetted: the bracing on the insides of the topsides and the underside boards. The latter was not done on the orignal build but, given the age of the boat and the fact that the majority of the hull timbers have been retained, made the installation of a strong fix, effectively holding the hull boards to the stringers, is a good precaution. Structural integrity has been the watchword of this restoration. I call it 'The Bay of Biscay Test'. This boat must be able to withstand the rigours of the kind of seas typified by the Bay of Biscay - short pitch, towering seas. If not, I have not done my job!
10th January 2023
The festive season is over. I spent most of the holiday on my knees – not in supplication, you understand – in Vera’s cockpit. Number three son (Andrew) was home from Canada for Christmas and, as well as the obligatory bottle of gin from Duty Free, he was required to give me a day’s work on Vera as an entry requirement. I had decided to rivet through the hull so as not to rely upon any original fixings holding the hull planking in place. I have replaced all the principal fasteners but just felt that some additional assurance that Vera will pass the ‘Bay of Biscay Test’ (i.e. not to fall apart in a heavy sea) was a good idea. For the riveting process two people are required – one in the cockpit doing the peening and the other lying underneath with the dolly. There are 224 rivets - copper boat nails – required and it took us about seven hours: five on Christmas Eve and two on Boxing Day. That’s my kind of holiday! I am not sure it is Andrew’s idea of a good time but he happily agreed and I am enormously grateful to him. (I should point out that his girlfriend, Dev – a Canadian – spent much of this time wielding a chainsaw on a pile of wood from the last tree that came down in the garden and splitting it into logs. Wonderful Canadians, eh? It would also be remiss of me not to mention that she painted the topcoat on the rear stringers, too. Thanks Dev.)
So once the riveting was done, I could get on with the focus of my Christmas break, which is painting the cockpit bilges. Some of you may recall the issues I have had with the bilges. During her former life, the port-side engine ‘shot a rod’ spilling engine oil throughout the bilges. When I first found Vera she had a mixture of engine oil, silt from Watchet Harbour and all the usual detritus that makes its way into a bilge, sloshing around below floor level. Cleaning this up so she will take a paint has been a gargantuan task. The bilges have been jet-washed, scrubbed, degreased, scrubbed again, and even wiped down with surgical spirit before and after sanding before all the oily residue had gone. Finally, I have a paintable surface.
I have chosen Epifanes as my paint of choice (coverage, bond, cost, range, availability, etc.) which is being supplied by Marine Industrial - www.marineindustrial.co.uk - and I have applied three coats of their multi-primer, reducing the thinning over subsequent coats, and two coats of bilge paint, in grey. A total of ten day’s work; uncomfortable but very, very satisfying.
So, after a relaxing holiday, spent almost entirely on my knees, I am delighted with the result. After five and a half years, this is the first bit of Vera that is ‘finished’!
Next up, I shall be installing the cockpit stringers, rear watertight bulkhead and some temporary sole-boards before looking forwards to six months flat on my back under Vera getting the undersides finished. At least I will be lying down…
February 2023
As pre-empted in the last update, in February, with the help of my eldest son, Fraser, we installed the cockpit stringers. These are critical structural elements of the boat; there is no keel, per se, only what is know as a ‘hog’, which is a relatively light-weight timber running along the keel line, incorporating the stem, into which the garboard planks are fitted. However, because it is only 1 ¾" thick at its thickest, it will not prevent the hull from flexing. This job is done by the stringers.
The stringers were built and dry-fit a couple of years ago – see Feb 2021, above – and have since been painted. We had to wait until the bilges in the cockpit were finished and painted prior to final fitting. Now that that has been done, I can finally stand at what will be, almost, finished cockpit floor level.
A previous owner had fitted a steel keel to Vera which I had removed prior to purchase. This left a dozen or so bolt-holes through the hog which had to be filled in a way that would not compromise strength. I fashioned some hardwood dowels that were driven through the holes and wedged, top and bottom, to ensure a tight and permanent fit.
Now I really have to get to those undersides...
July 2024
I have a new helper! His name is Mike and he was introduced to me by my aunt, Neash.
Mike has form - he lives on a boat which he built himself.
He comes one day per weekend but in the short time he has been coming, he has proved himself to be invaluable. I set him the task of planking the transom which, after a little instruction and introduction to some new tools - my much-treasured compass plane for one - he has done an excellent job.
So now Vera has a complete, although dry-fitted, transom. Before I can finally fix the transom, I am waiting on the new rudder assembly that is being cast for me by Irons Brothers of Wadebridge. I was given the full tour of the site when I went down there in May; it is a fantastic, old-fashioned business casting iron and bronze in exactly the same way it has been done for centuries. They still make cannons!! I am delighted that there will be a bit of traditional British manufacturing on Vera. As a note, the other company I approached for this work out-sources it to China. Shame.
Alongside building the transom, Mike and I have been fairing the undersides; they're now pretty close. As ever, various jobs have to be completed before another can start. Or possibly vice versa - various jobs have to be started before another can be finished - and that is how it is with the undersides.
One of the other jobs has been making and fitting the chine rubbing strakes - very important to protect the chine, just above and below the waterline. I made the decision to scarf the individual timbers together on the workbench and fit it as a single piece. This will ensure a lovely sweeping curve from stem to stern. I didn't consider how challenging it would be to manually handle a 42-foot length of timber but with ingenuity, clamps and saw-horses, we overcame the obstacles.
As you will know by now, I am not big on power-tools - I much prefer the manual version - but putting the roundover on the rubbing strakes called for serious power. I acquired a massive 1"1/2 radius cutter that said it was for 'fixed machinery only', but not having a fixed machine, I stuck it into a portable router and hoped for the best! Thankfully, it went well, no-one was injured and the result was fab! The port-side strake was dry-fitted last weekend and we'll do the starboard next weekend.
So what's on the horizon?
Next up, I think, will be the gunwale rubbing strakes but in order to do that, I have to fit the (temporary) coverboards, which are made but not fitted, and that will take a little fettling to make sure they are 'true' to the deck structure. The intention is to install these strakes in much the same way, as a single long lengths. It makes handling the piece more difficult, but the result will be much better. There are a few steps in the process, each fraught with potential pitfalls, but that is all part of the fun!
November 2024
Aft Peak/Lazarette
OK, so I didn’t do the rubbing strakes… In September, I got the beautifully replicated rudder back from Irons Brothers in Wadebridge, Cornwall. When I first acquired Vera, she had mis-matched rudders – one was original and ‘correct’, while the other was smaller. Irons Brothers, a traditional foundry, made a cast from the original rudder and created a perfect replica so I now have two matching rudders.
In spite of other works ongoing, as soon as I got the rudders onto the workshop, I knew I was going to fit them immediately. I had photos of the rudder block arrangement from when Vera was new to me, but it was obvious that there had been a fair bit of butchery since she was first built, so using the 1941 layout drawings and some common sense, I went about re-boring holes through the new underside planking and creating top and bottom mounts for the rudders. In light of Vera’s age, it felt like a good idea to beef-up the bracing a bit, but otherwise, this is now how she would have been laid out originally.
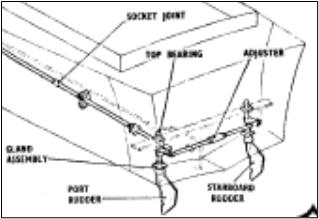
I had a slight issue to overcome; when I got Vera, she had a single-piece tie-bar between the two rudder arms, and to fit it, a previous owner had cut away large sections of the stringers, thereby reducing the strength of this important structural element, so I have charged my faithful metalworker, Paul, with making a two-part tie-bar with a central bottle screw for adjustment – as would have been originally specified – evidenced on the drawings.
Now that the rudders have been installed – still waiting on the tie-bar – I am ready to final-fix the transom. I was aware that access to the aft-peak would make fitting the rudders much easier and have held-off the final fit. However, since I currently have access, this is also an excellent opportunity to do any other works in the area. One of the things that wasn’t originally specified, was any separation between the upper area of the aft-peak and the lower part, where the rudder gear is. This separation is important to make the lazarette a usable locker space. I have built some framing around the space and installed removable hatch covers.
Now, with the rear bulkhead shaped and installed, I am ready to remove everything I have done and paint it all prior to final installation, at which point I can finally fix the transom and have a complete (more or less) hull.
Over the years, I have read, or heard anecdotally, about how notoriously heavy the steering was on these craft. Now that I have installed the rudders – and not yet the through-glands, guide-wheels or worm-gear – I am getting an appreciation of this. Admittedly, no lubrication is yet present, but just moving the rudders alone is pretty heavy. I do have the option of switching to a Bowden cable arrangement and I might choose this option. It won’t be original but will be so much more practical. I can still retain the original worm-gear (Bishop, off an MG A, I understand) and it will take so much of the friction out of the steering system. Tempting…